Biological Safety Cabinets
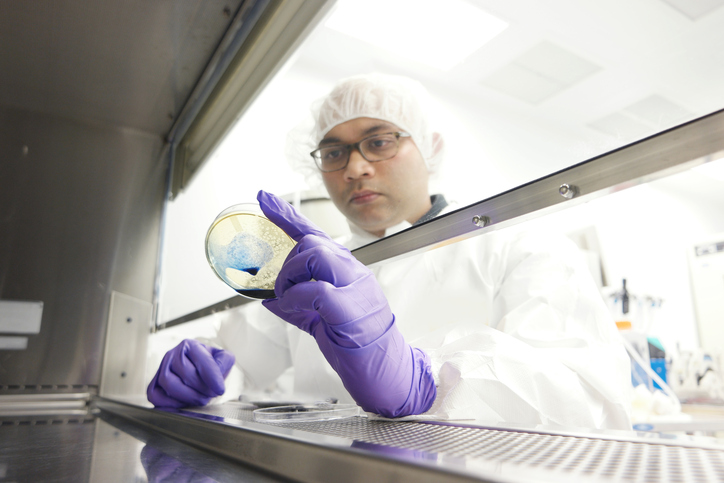
Updated June 28, 2024
Biological safety cabinets (BSCs) are used to protect personnel, products and the environment from exposure to biohazards and cross contamination during routine procedures.
Classes of biological safety cabinets
When choosing a biological safety cabinet for your work space, Environmental Health & Safety (EH&S) can help you select the class of cabinet that will provide the best protection.
There are three classes of BSCs: Class I, II and III. While all three classes afford personnel and environmental protection, only Class II and III cabinets provide product protection.
- Class I BSCs are suitable for work involving low to moderate-risk agents. Since incoming air is not filtered, Class I BSCs should not be used with research materials (e.g., cell lines) that must be handled under sterile conditions. Class I cabinets are used to enclose equipment (e.g., centrifuges, harvesting equipment or small fermenters) or procedures with potential to generate aerosols (e.g., cage dumping, tissue homogenization or culture aeration). Because outgoing air is filtered, research personnel are protected while using a Class I BSC.
- Class II BSCs provide a partial barrier for the safe manipulation of low, moderate and high-risk microorganisms. Class II cabinets, which are the most frequently used in research and clinical laboratories, are divided into four types (Types A1, A2, B1 and B2).
- The Class III BSC is a totally enclosed, gas-tight ventilated cabinet, and provides the highest level of personnel, environmental and product protection. Operations within a Class III BSC are conducted through attached rubber gloves.
Selecting a biological safety cabinet
When purchasing a biological safety cabinet, you should consider the type of work that will be conducted in it.
Table 1 describes the principal characteristics of all classes and types of BSCs.
BSC CLASS/TYPE
|
PRODUCT PROTECTION
|
MINIMUM FACE VELOCITY (FPM)
|
VOLATILE TOXIC CHEMICALS, GASES OR RADIONUCLIDES ALLOWED?
|
---|
I
|
No
|
75
|
No
|
II / A1*
|
Yes
|
75
|
No
|
II / A2
|
Yes
|
100
|
No, unless thimble connected to the HVAC system, then low levels of volatile toxic chemicals allowed
|
II / B1
|
Yes
|
100
|
Yes: low levels of volatile toxic chemicals & trace radionuclides
|
II / B2
|
Yes
|
100
|
Yes: volatile toxic chemicals & radionuclides
|
III
|
Yes
|
N / A
|
Yes
|
Table 1: Characteristics of different classes and types of BSCs
*These cabinets are obsolete; no parts are available to repair the cabinet.
For more information, please read the Chemical Use in Biological Safety Cabinets Focus Sheet.
What you need to know
Contact EH&S if you plan to purchase or relocate a biological safety cabinet, or bring a unit to the UW from another university. EH&S can help you select the appropriate cabinet for your research, evaluate the space you are considering, and determine if necessary ventilation and utilities are available. Review the Steps to Purchase, Replace, Relocate or Remove a Biosafety Cabinet for more information.
Your cabinet needs to be tested and recertified annually by a qualified EH&S safety professional. If EH&S has your cabinet in its inventory, we will contact you about a week in advance of our service.
If your cabinet sounds an alarm or does not appear to be functioning as intended, stop your work and contact EH&S for assistance.
Services available
EH&S provides the following services:
- Performs certification service for biological safety cabinets to verify and assure proper performance; BSCs are tested to manufacturer's specifications and to National Sanitation Foundation Standard 49.
- Maintains design standards for new construction and provides consultation on cabinet selection, performance, decontamination, relocation and design.
- NSF required Gaseous Formaldehyde decontamination of the cabinet prior to service, relocation or surplus.
Frequently asked questions
The technician assigned to your area will contact you to schedule the certification. You will need to clear out the cabinet, provide the technician with a budget number for the service and notify other users that the certification is occurring.
When the technician arrives, they will bring a cart with testing equipment into the area where the BSC is located. There is no predetermined length of time it takes to perform the certification; the duration of time varies according to the cabinet type, size and number of adjustments. You can contact the technician with any questions about timing and logistics.
The technician will perform the following certification tests:
- Supply airflow (downflow) calibration
- Exhaust airflow (inflow) calibration
- Supply and exhaust HEPA filter integrity
- Visual smoke patterns
- Site installation assessment
After the certification is complete, the technician will inform the lab and share any findings related to the certification, including optimizing the cabinet design and performance. A certification report will be sent by email to the laboratory contact. This report will also serve as the billing document.
EH&S regularly reviews the fees for services we provide to users of biological safety cabinets (BSCs) to ensure our fees match the expenses we incur for these services.
The table below shows rates for BSC services provided by EH&S that are in effect from July 1, 2024 through June 30, 2025.
SERVICE
|
FY24 FEE
|
NEW FY 25 FEE
|
BSC Certification Test |
$446.00 |
$449.00 |
BSC Airflows Only |
$168.00 |
$196.00 |
BSC Filter Test Only |
N/A |
$196.00 |
BSC Decontamination for Relocation |
$504.00 |
$588.00 |
BSC Decontamination for Motor Change |
$504.00 |
$588.00 |
BSC Decontamination for Filter Change |
$504.00 |
$588.00 |
BSC Decontamination (Unspecified) |
$504.00 |
$588.00 |
BSC Filter Fail Change and Retest |
$0.00 |
$0.00 |
BIBO (bag-in/bag-out) Decontamination-Certek, Filter Scan |
$672.00 |
$784.00 |
BIBO Decontamination-No Certek, Filter Scan |
$252.00 |
$294.00 |
BIBO Filter Change, Filter Scan |
$0.00 |
$0.00 |
Other Service - per Hour |
$84.00 |
$98.00 |
Biosafety cabinets generally have two HEPA filters: The Supply filter, which filters the flow of air onto the work surface for product protection; and the Exhaust filter, which filters the air that leaves the BSC for environmental and personnel protection. There are 3 basic parts of the process to get new filters.
1. Order the correct filters.
- The technician responsible for your cabinet will provide the specifications needed to order your filters and from whom to order; either the cabinet manufacturer, or a third party vendor.
- Information provided includes the model and serial number of the cabinet. This insures the correct filter is sent from the factory/vendor.
- Payment and delivery of the filters are the responsibility of the lab and the filter supplier. It is best to keep the BSC technician informed of process for scheduling purposes.
2. Arrange a time for the decontamination of the BSC.
- Once a delivery date has been provided to you by the filter supplier, make contact with the technician responsible for your cabinet to arrange for decontamination, filter change and re-certification of your BSC. This ensures lab personnel are informed of the procedure as the paraformaldehyde decontamination phase typically restricts access to the lab.
- The BSC cannot be used during this process.
3. Filter change and re-certification of the BSC.
- Cabinets require extensive disassembly to access the filters, so the area where the cabinet is located should be reserved for EH&S during this time.
- The old filters are removed and disposed of, and new filters are installed. The cabinet will be certified at this point.
Most filter replacement procedures require about 24 hours over three days: Afternoon on the first day, all day on the second day, and filter change/re-certification on the morning of the third day.
EH&S requires paraformaldehyde decontamination when a BSC needs service, such as:
- BSC is scheduled to have filters replaced
- Motor or electrical component service that requires access to contaminated locations
- BSC will be moved to a different location
- At the request of the lab
In the event of filter or component failure, the technician will contact you to schedule the decontamination. If you would like to request decontamination of your BSC in order to have it moved or another reason, please contact the Lab Safety Team at labcheck@uw.edu. Provide your technician a budget number for the service and notify other users with the scheduling details for the decontamination.
Prior to your scheduled decontamination, you will need to clear out the cabinet, including under the worksurface and perform your routine surface decontamination. Clear the area around and under you BSC of chairs, waste containers, vacuum pumps or any other items that may impede technician access to the cabinet.
The decontamination process occurs over approximately 24 hours; access to the area where the BSC is located may be restricted during this process. EH&S will post signage indicating restricted access as appropriate, including the duration of time access to the area is restricted.
The technician will perform the following decontamination steps:
- Power to the BSC will be shut off.
- The BSC will be enclosed with durable plastic sheeting and duct tape.
- A cart (approximately 20 by 30 inches) with the decontamination equipment will be located as close as possible to the BSC.
- The equipment will be powered on and the process will be timed to ensure complete decontamination and neutralization of the agents used for decontamination.
- After the decontamination has ended, the technician will return and vent the BSC, either by using the canopy, if available, or a nearby source of ventilation, such as room air exhaust or a fume hood.
When the decontamination and venting of the BSC is complete, the technician will inform the lab and provide documentation (affixed to the BSC) confirming the decontamination has been performed.
For information on replacing obsolete biosafety cabinets, please refer to the following resources:
EH&S does not prohibit UV light and you may choose to include a UV light when ordering a BSC. However, it is our opinion that is not necessary nor recommended in biosafety cabinets.
The EH&S annual certification of the cabinet does not include a verification of the efficacy of the UV light.
For more information, read "Position Paper on the Use of Ultraviolet Lights in Biological Safety Cabinets" (Burgener, July, 2006, Applied Biosafety, 11(4) pp. 228-230, and the article The trouble with UV light in your biosafety cabinet.
Laboratories can experience ventilation shutdowns. These shutdowns can be the result of planned maintenance work as well as unplanned events such as equipment failure or power outages.
Do not use biological safety cabinets (BSCs) with canopies when the ventilation system serving a room is not functioning. This applies to both supply air as well as exhaust air. Inadequate ventilation associated directly with your equipment or indirectly with your room can compromise personal protection. The product protection provided by a BSC can also be compromised.
If you have concerns regarding your biological safety cabinet during a shutdown or need help troubleshooting issues with your equipment, contact Environmental Health & Safety at 206.543.9510.