Emergency Washing Equipment
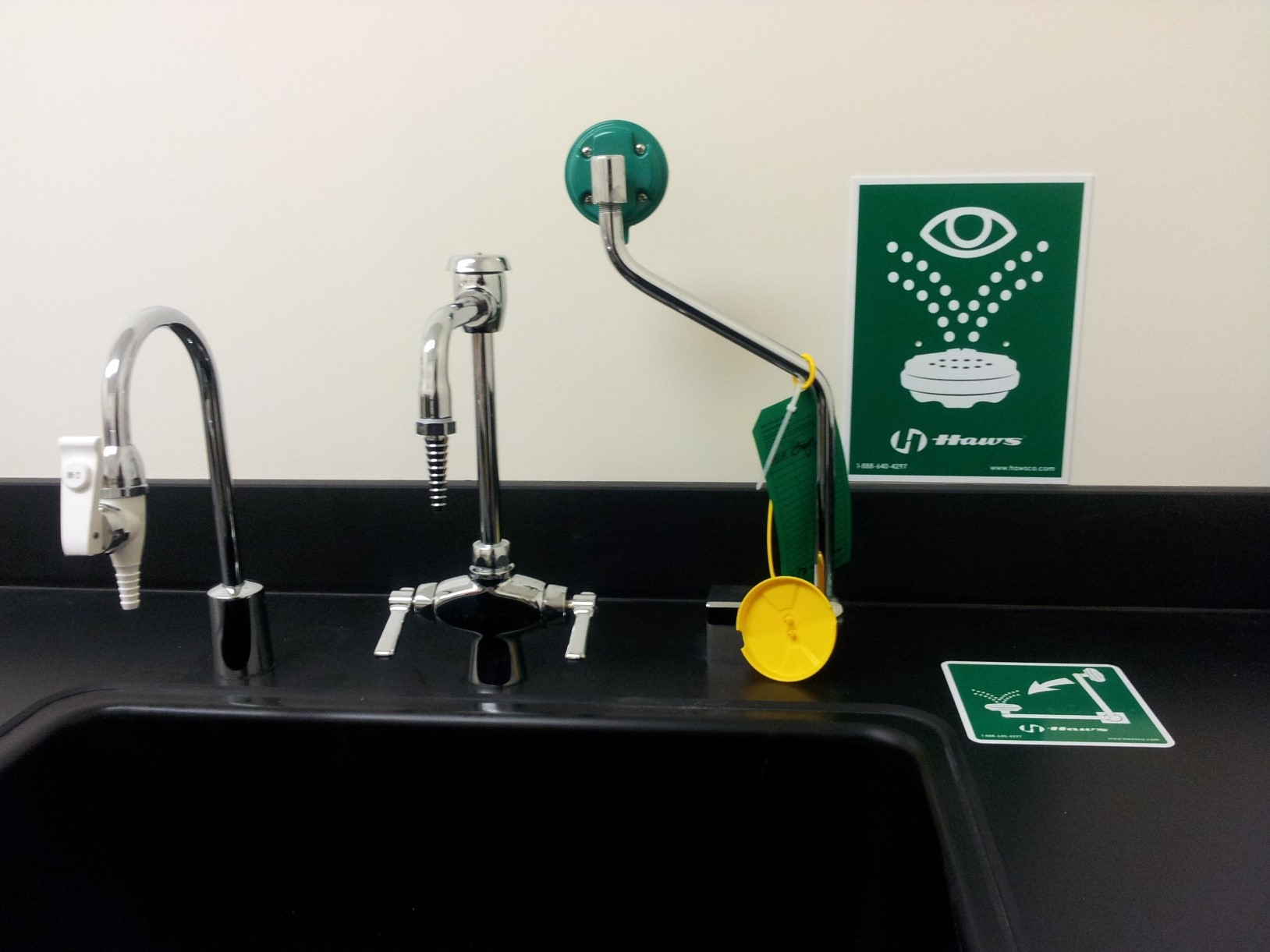
Updated October 3, 2024
Emergency washing equipment is provided in University facilities for the purpose of removing hazardous materials from the eyes and skin in the case of an exposure. Examples of emergency washing equipment are listed below.
Eyewashes are required in existing areas where any of the following hazardous materials are handled:
- Chemicals that are corrosive, strongly irritating, and/or toxic when absorbed through the skin
- Biological hazards that require biosafety level 2 (BSL-2) or animal biosafety level 2 (ABSL2) and higher
- Unsealed sources of radioactive materials
Eyewashes are required in these additional areas when they are located in new construction or areas that undergo major renovations:
- Spaces operating at biosafety level 1 (BSL-1) or animal biosafety level 1 (ABSL1) and higher
- Areas where airborne particles are generated (such as wood dust)
A drench hose is an emergency washing device connected to flexible hose used to irrigate and flush the face or other parts of the body. Drench hoses may serve as an eyewash if installed in the proper location and with the proper eyewash attachments; however they are not a replacement for emergency showers in areas where they are required.
An emergency shower is required in areas where any corrosives, strong irritants or toxic chemicals are used in quantities and processes that could result in a substantial portion of the body being impacted.
Exposure response and reporting
Make sure you know where the nearest emergency washing equipment is located and how to use it in an emergency.
In the event of an exposure to hazardous materials, follow the steps in the Exposure Response Poster.
It is recommended that groups stock spare clothing that can be used to cover up after using the emergency shower.
UW personnel are required to submit an incident report to Environmental Health & Safety for any work-related event that results in an injury, illness, exposure to hazardous materials, or fire. UW personnel are highly encouraged to submit reports of near-miss events.
What you need to know
Does your work involve hazardous materials or activities that require emergency washing equipment? If yes, verify the following:
- It is the correct equipment. (Contact us to request an evaluation.)
- It is accessible.
- The equipment is properly maintained.
- You know where it is located and how to use it in an emergency.
Ask your supervisor about the location and specific function of emergency washing equipment in your work location.
- If you work in a laboratory setting: Additional information on the use of emergency washing equipment is included in the Managing Laboratory Chemicals Online course. This course is required for University personnel who work in laboratories where hazardous chemicals are present.
- If you work outside of a laboratory setting: Reference the Eyewashes and Safety Showers Training Online course for information on the use of emergency washing equipment. Your supervisor may require this training depending on your job tasks and responsibilities.
NOTE: Supervisors must document that they have provided training on the location and use of emergency washing equipment (and other emergency equipment such as first aid kits) to personnel that they oversee.
To be accessible, emergency washing equipment is required to be:
- Free of physical obstructions that inhibit use
- No greater than 50 feet travel distance from the process of concern
- Along a path of travel without obstructions
Emergency washing equipment does not replace the requirement to wear eye and face protection and other personal protective equipment when working with hazardous materials that can present an exposure potential to the eyes and body.
Weekly testing
Departments/units are responsible for activating the eyewash and drench hose equipment once per week to verify proper operation. The weekly eyewash test ensures that the unit is providing clean water at suitable pressure.
- The eyewash must be operated for approximately 30-60 seconds.
- The water should run clear and should reach a height that would allow for both eyes to receive adequate coverage.
These weekly tests are required to be documented. Documentation can be physical paper or virtual sheets accessible through QR code but must be accessible to personnel at the site of the equipment.
UW Facilities (on the Seattle campus) or your campus facilities group is responsible for testing safety showers annually to verify proper operation.
Services available
Environmental Health & Safety (EH&S) provides the following services:
Frequently asked questions
Environmental Health & Safety regularly conducts evaluations of emergency washing equipment in research laboratories, shops, and maker spaces as part of its routine inspection programs.
- If you have questions regarding emergency washing equipment access, contact us to request an evaluation.
- If you work outside of lab, shop, and maker spaces, or you are adding new processes or hazardous materials to your space that may warrant emergency washing equipment installation, contact us to request an evaluation.
Your supervisor is required to train you on the specific location and use of emergency washing equipment in your work locations(s). This should be included as part of your onboarding process. All site-specific training and orientation is required to be documented. Ask your supervisor if you have questions about the location and specific function of emergency washing equipment in your work location.
If you work in a laboratory setting, additional information on the use of emergency washing equipment is included in the Managing Laboratory Chemicals Online course. This course is required for University personnel who work in laboratories where hazardous chemicals are present.
If you work outside of a laboratory setting, review the Eyewashes and Safety Showers Training Online course for information on the use of emergency washing equipment. Your supervisor may require this training depending on your job tasks and responsibilities.
Eyewashes and drench hoses are required to be tested and documented weekly. Refer to the instructions on this page for more information.
Responsibility for weekly eyewash testing varies by location; however, it is generally performed by the room occupants. Ask your supervisor or building/facility manager if you are not sure who is responsible for this task in your space.
Place a request through your facility’s work order system to have it evaluated and repaired. Contact UW Facilities on the Seattle campus.
Emergency shower (and more extensive eyewash) testing is performed on an annual basis by facility personnel.
Definitions
Chemicals that cause destruction of living tissue by chemical action. Includes acids and caustics with a pH equal to or less than 2.5 or greater or equal to 11; designated under the Globally Harmonized System as Category 1 under the hazard class “skin corrosion/irritation” or Category 1 under the hazard class “serious eye damage/eye irritation.”
Chemicals that induce local inflammatory reaction on the cornea, iris, or conjunctiva and are designated under the Globally Harmonized System as Category 2A under the hazard class “serious eye damage/eye irritation
Chemicals that are toxic or highly toxic and can be absorbed through the skin. Designated under the Globally Harmonized System as Category 1, 2, or 3 under the hazard class “acute toxicity, dermal”